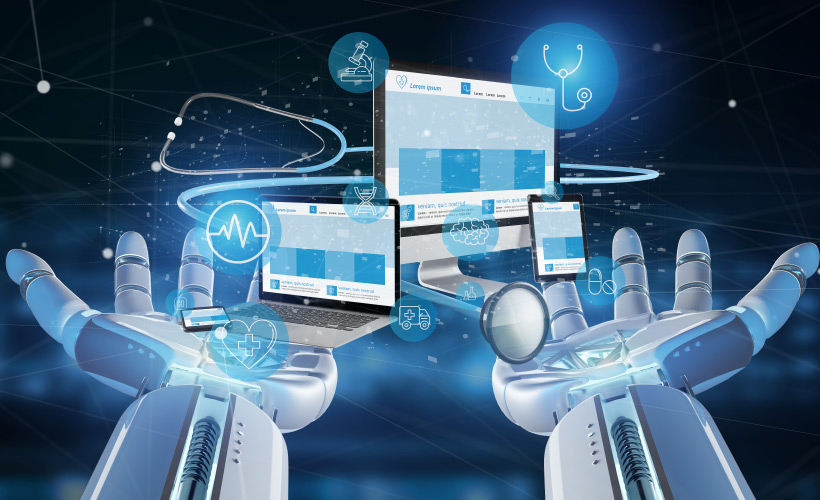
What Is Risk Mitigation for Medical Device Packaging?
Medical device packaging risk mitigation involves evaluating the medical device packaging process, determining where there are gaps or potential opportunities for critical issues to be missed or overlooked, and then identifying the most economical and effective way to ensure that those opportunities are eliminated or minimized.
The most vital areas of the medical device packaging process that must be evaluated include the packaging itself, creation of a seal/sterile barrier, insuring that the correct item(s) are in the pouch, labeling, and the inspection process—all of which are essential for ensuring that the end-user receives the correct product, sterile and intact, with the correct labeling and information. When medical professionals are working in the clinical setting, they need to identify medical devices quickly.
These packages must be sealed in a way that maintains sterility, and they must be visibly, legibly, and correctly labeled. In addition, the packages must be able to be easily opened so that the product can be removed in a controlled manner.
What are the key issues medical device manufacturers need to consider with regard to risk mitigation for medical device packaging?
One of the key issues to consider is validation. The packaging process for medical devices must be validated as robust and repeatable, so that operators can complete the executable actions in the correct order, accurately, over and over again. Because the packaging process typically involves manual steps, however, unforeseen or unexpected interruptions in the flow can occur.
For instance, when an operator packages a medical product into a pouch, they typically pick up the product, and then pick up then pouch. Next, they place the product into the pouch, and then take the pouch to a heat sealer where they apply a seal. Lastly, after the pouch is sealed, they visually inspect the package before putting it into the good disposition bin or placing it onto a take-away conveyor. If the operator is distracted during any one of these steps, errors can occur.
The incorrect product could be put into the pouch, the product could be put into the pouch in the wrong orientation or the wrong pouch could be used. In addition, the seal could be imperfect or missing entirely and/or the packaged could be labeled incorrectly. Engineers need to think through all of these possibilities and determine the best ways to prevent these kinds of mistakes. They need to understand where there are gaps in the packaging process and what the risks of these gaps are, and then work to mitigate those risks.
Why is risk mitigation important?
Risk mitigation is important because if medical devices are not properly packaged, patients can be injured or even die. According to an FDA study, there were more than 1.7 million preventable injuries and nearly 83,000 deaths associated with medical devices over a 10-year period.
Risk mitigation in medical device packaging diminishes significant business risks. If an issue with the packaging process is documented as a recurring issue, the device manufacturer could have to recall the product(s) in question. Recalls are typically costly to conduct, and there are additional costs associated with remediation steps and ensuring that the problem doesn’t happen again. Medical device manufacturers can also suffer loss of sales revenue during remediation and considerable reputational damage.
What aspects of packaging should a medical device manufacturer review to mitigate risk?
Medical device manufacturers need to review several different aspects of packaging in order to mitigate risk. For instance, one of the most critical aspects to review is the seal on the package. Medical devices requiring sterility must be packaged with a hermetic seal. This type of seal creates a barrier that prevents microbes from infiltrating the package during the shelf life of the product. To maintain sterility, the seal cannot be weak or incomplete.
Creating a hermetic seal on pouches involves properly aligning the packaging materials in the sealer and then correctly applying the seal. Likewise, for medical devices sealed in tray, the tray must be properly presented to the sealer and the seal must be correctly applied.
Other aspects that need to be reviewed to mitigate packaging risk include ensuring that the correct product and the correct quantity of product is packaged as well as that the product is identified and labeled accurately. Many companies mitigate packaging risks by conducting a “line clearance” between lot runs. That means they completely clear the line of all products, packages, labels, and IFUs between runs. Then, they bring back in only what is needed for the new run.
What process should engineers follow when designing risk mitigation for medical device packaging?
In some cases, engineers begin the process of mitigating risk by taking a historical approach, comparing a new or proposed packaging process to one that the company already is using successfully.
For instance, if the medical device manufacturer is currently packaging a similar product of similar weight, similar barrier requirements, with similar packaging material, or using the same sterilization methods, it can be beneficial to leverage this history. In other cases, it may be more advantageous to disregard history and instead, evaluate the new or proposed project on its own, without any prior assumptions.
Often, it’s a combination of the two approaches that is most effective. For example, if two different products use the same pouch, it may be helpful to look at historical data regarding how the pouch materials perform under specified sealing conditions. However, if the products differ in weight, the seal performance characteristics are likely to be quite different with each requiring its own unique process.